Learn how to apply simple improvement methods to eliminate your most frustrating problem at work. We provide short instructional tips filled with helpful direction, templates and an attached e workbook filled with tools and tips. And it’s all free! Workbook
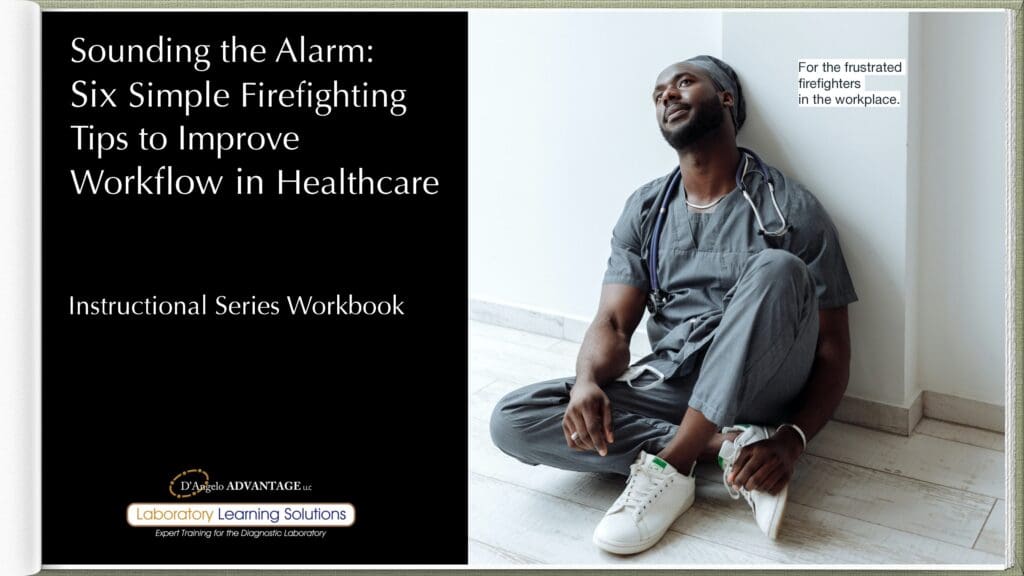
SOUNDING THE ALARM. SIMPLE FIREFIGHTING TIPS TO IMPROVE YOUR WORKFLOW
INTRODUCTION:
Are you frustrated at work? Are you fire fighting just to get your work done? The heat is on for healthcare professionals who are fighting fires while meeting the demands of the job. If so, join laboratory learning solutions for a free series called Sounding the Alarm- Firefighter tips to improve your workflow. We offer six simplistic tips to guide you to make improvements that will remove bottlenecks and gain operational efficiency in your workplace. This proven series teaches you how to effectively identify sources that fuel the chaos and present solutions to promote workflow improvements. With these simple steps, you and your team can extinguish the avoidable firewalls and focus on the tasks at hand. Join us on this journey to learn free firefighting tips!
TIP # 1-WHAT IS GOING ON HERE?
We begin our firefighting series with Tip # 1. What’s going on here? To begin, we gather the team and pose the question: What issue during your workday requires you to stop your work and fix some thing before you can continue? Give the team a few minutes to reflect on their workday and capture the team response. Gather one frustrating issue per team member. Once the list is complete review the issues with the team and ask: how often do these issues happen in any given day? Record responses and add a number next to each issue on the list. The perspective from each effected employees is critical considering they perform the rework. Next, take a vote from the team. Review the entries on the list and based the frequency, ask the team which issue should we work on first? Which one has the highest number of issues occurrences? Which issues is affecting workflow? Which issues may affect the integrity of the work. Lastly, decide as a team: What will we work on? Choose one. This concludes Tip # 1.
TIP # 2-UNDERSTANDING THE REAL ISSUES
In our first session within the series, What is going on here? we reviewed the list of team member frustrations and chose one. We will now brainstorm that issue with our team to determine the causes. The tool we will use is called a Fishbone or Ishikawa. The goal of the fishbone is to understand every contributing factor to our issue and reasons for occurrence by using the 5 Why’s to drill down to the root cause. (There may be 3 or 4 whys to get to the root cause). In this fishbone we listed the typical categories such as ,management, man, method, environment, machine and material. However, you can list any category that fits your purpose. To get started we listed the issue. For learning purposes, we will use missing information as our issue. Now lets begin with the category – management. Are there any contributing factors from management that may be problematic in this process. Yes, management doesn’t hold employees accountable for defective work that is passed off. Now lets ask the 5 Why’s. Why doesn’t management hold employees accountable? Because they don’t see what is happening, Why doesn’t management see what’s happening? Because they don’t walk through. Why don’t they walk through? Because there is a team lead in that area but, the team lead is called away most of the day. Now we can see the contributing factor number 1. The employees work includes missing information because no one observes or corrects their work. To learn more about why these issues happen, go through each category until the fishbone is complete. You have a good understanding about why these occurrences happen. This concludes tip number 2. Join us for Tip number 3. We will go to the place where the work is happening and learn more. See you there
Tip #3: Observing the Process
In Tip 3 of the Firefighting Series, we describe the process of observation in the workplace. We go to the place where the work is occurring to see for ourselves what is happening. We follow the process from start to finish and document any activities that may have contributed to our original issue. Waste, inefficiency, and defects are noted, complied, and shared within the team. We identify common problems and create a list for use in the next phase of the series.
Tip #4: Documenting a Few Steps of the Process
In Tip 4 of the Firefighting Series, we create a high-level process flow consisting of 5 steps from a call center to note how our original issue, missing information, actually happened. The process begins with a call from the customer and ends with the customer receiving the service. By studying this process flow we grasped the handoffs, bottlenecks, defects and what happens from start to finish. We note a total processing time of 5 hours. During this high-level map we have identified a few process steps and corresponding issues that happened between those steps. We noted these as defects in the process or reasons for missing information that we call opportunities for improvement. These defects may have contributed to our original issue so we added them to the bursts above.
During Tip number five, will work on one opportunity for improvement. The goal is to re-design the process so that root cause is eliminated and the process is more efficient. In preparation for Tip number five, choose one step in the process with a corresponding opportunity for improvement. We’ll learn how to eliminate that defect and redesign the process.
Tip #5: we can design a more efficient process
In Tip # 5- we discuss designing a more efficient process. We learned that the outcome of our issue, missing information, resulted in daily firefighting that included lack of management support, rework, waiting, customer dissatisfaction and the list goes on. We noted opportunities or defects that occur within our 5-step flow and chose step # 2 to start the improvement process. The order is entered into the system and data fields missing from the order form is our corresponding defect. The opportunity here is to redesign the electronic form to improve all submissions. Once we redesigned the form, we saw significant improvements. – 50% reduction in turnaround time. We eliminated the flagging missing data, missing fields on the form and the orders are no longer being flagged or placed on hold. Results: Happy Team!
TIP # 6- OK. That Worked so WHAT’s next?
Tip # 6-In this final firefighting tip, we discuss continuing with the improvement process. We revisit the original process map, choose another kaizen burst, brainstorm with our team and work to eliminate this issue from reoccurring. Once again, we will follow the identical method and work to eliminate the remaining issue of management not present in the work area. We’ve learned a simple method to improve healthcare processes and reduce the frustration and firefighting within our daily work. Lastly, we learn to celebrate our hard work and success!