Fast Track: A3: Problem Solving in Healthcare
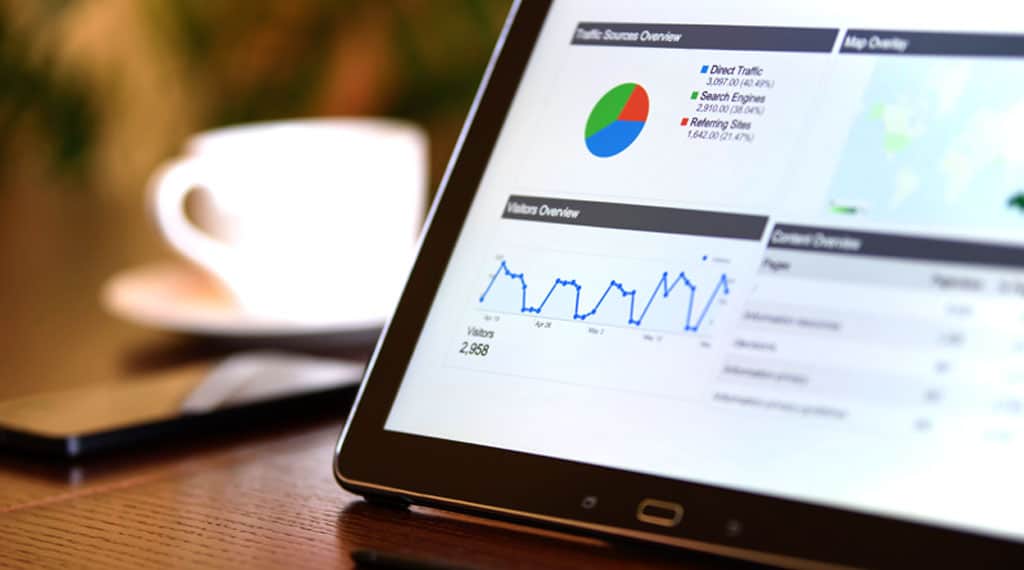
Price: 29.99
Description
3.0 Contact hours ($29.99)
Welcome to the A3 Method for Problem Solving!
A3 Problem Solving is a structured, team-based approach that uses data and process analysis to identify root causes and implement effective solutions. This method follows an 8-step process, documented on a single-page report. The left side outlines the Current State, while the right side defines the Future or Desired State. In this course, you will learn how to execute each step, systematically improving processes and driving lasting solutions through collaborative problem-solving.
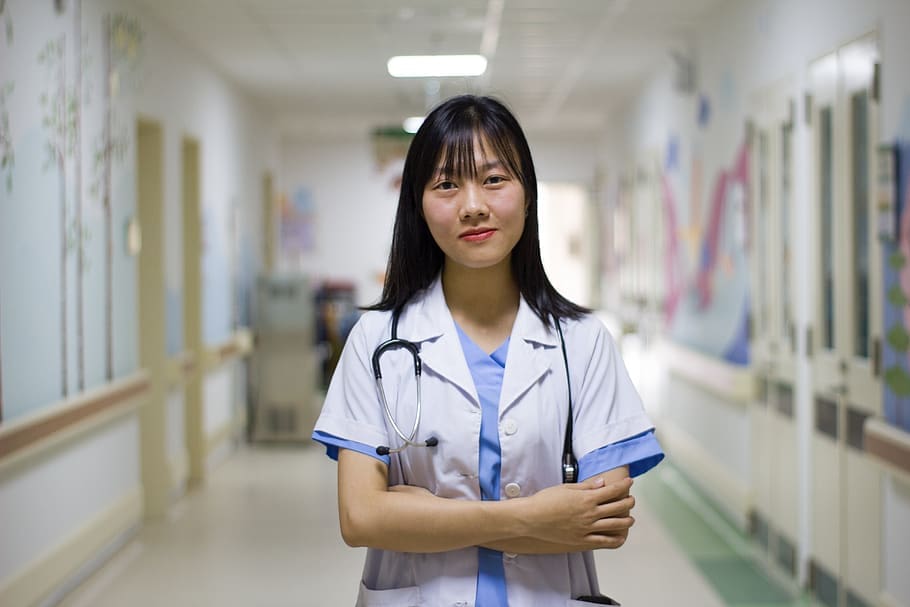
This Course Includes:
The course is presented in 7 lessons:
- In the Introductory lesson you will learn the back story and logic behind using the scientific method for problem solving.
- Unit 1 (Lesson 2) covers team development and the problem statement.
- Unit 2 (Lesson 3) is devoted to describing the current state.
- Unit 3 (Lesson 4) details finding and analyzing causes and is the longest lecture at 25 minutes.
- Unit 4 (Lesson 5) includes describing the target condition and identifying solutions.
- Unit 5 (Lesson 6) will help you develop an implementation plan and set up effectiveness checks.
- Unit 6 (Lesson 7) is the final unit and covers techniques for holding your gains.
In this course, you will learn how to apply the A3 method to a process of your choosing and complete each section of the A3 form. It would be helpful for you to print out the form using the template provided and practice each step as we proceed
The Course Structure
The following is included in this course:
- Seven engaging instructional videos
- Quiz-10 questions
- An assignment is not required
At the End of this course the learner will be able to:
- Follow A3 background/logic
- Evaluate/interpret each A3 element
- Complete an A3 form, organizing each element of the A3 method
- Integrate common A3 tools: process flow diagrams, five why problem solving, causal analysis tools, and Plan–Do–Check–Act (PDCA cycle)
- Completion of a quiz is required to obtain a certificate of completion and credit hours.
- Completion of a quiz is required to obtain a certificate of completion and credit hours.
References and additional reading for this course can be accessed using the “Materials” tab at the top of the Course page.
References for A3 Problem Solving in Healthcare
All units: American Society for Quality. “Quality Glossary.” Retrieved from https://asq.org/quality-resources/quality-glossary. Accessed August, 2020
All units: Drickhamer, D. “View from the hospital floor: how to build a culture of improvement one unit at a time.” Retrieved from https://www.lean.org/common/display/?o=3207. Accessed March 2020.
All units: Institute for Healthcare improvement. “Quality improvement essentials toolkit.” Retrieved from http://www.ihi.org/resources/Pages/Tools/Quality-Improvement-Essentials-Toolkit.aspx. Accessed March 2020.
All units: Tague, N.R. (2005) [1995]. The quality toolbox (2nd ed.). Milwaukee: ASQ Quality Press. pp. 390–392.
Introduction: Cusumano, M.A. (1985) The Japanese automobile industry: technology and management at Nissan and Toyota. Cambridge, MA: Harvard University Press.
Introduction: Deming, W. E. (1986) Out of the crisis. Cambridge, MA: Massachusetts Institute of Technology, Center for Advanced Engineering Study.
Introduction: Liker, J.K. (ed.) (1998) Becoming lean: inside stories of U.S. manufacturers. Portland, OR: Productivity Press.
Introduction: Sobek II, D. K. and Smalley, A. (2011) Understanding A3 thinking: a critical component of Toyota’s PDCA management system. New York: Productivity Press.
Introduction: Sobeck II, D.K. “The A3 Report.” Retrieved from http://www.montana.edu/dsobek/a3/report.html. Accessed August, 2019.
Introduction and Unit 4: Womack, J.P. and Jones, D. (1996) Lean thinking: banish waste and create wealth in your corporation. New York: Simon & Schuster.
Introduction and Unit 4: Womack, J.P., Jones, D. and Roos, D. (1990) The machine that changed the world: the story of Lean production. New York: Harper Colins.
Unit 1: US Department of Veteran’s Affairs. “43. SIPOC (suppliers, inputs, processes, outputs, customers)” Retrieved from https://www.queri.research.va.gov/implementation/quality_improvement/methods.cfm?method=43.
Accessed March, 2020.
Unit 2: Millard, M. Krainexus. The top ten worst things you could do on a Gemba walk. Retrieved from https://blog.kainexus.com/improvement-disciplines/lean/gemba-walk/the-top-ten-worst-things-you-could-do-on-a-gemba-walk. Accessed March, 2020.
Unit 2: Institute for Healthcare improvement. “Quality improvement essentials toolkit —Pareto Chart.pdf” Retrieved from http://www.ihi.org/resources/Pages/Tools/Quality-Improvement-Essentials-Toolkit.aspx. Accessed March, 2020.
Unit 2: Institute for Healthcare improvement. “Quality improvement essentials toolkit—run chart and control chart.pdf” Retrieved from http://www.ihi.org/resources/Pages/Tools/Quality-Improvement-Essentials-Toolkit.aspx. Accessed March, 2020.
Unit 3: Balle, M and Jones, D. “10 signs you respect me as an employee.” Retrieved from https://www.fastcompany.com/3036623/10-signs-you-respect-me-as-an-employee. Accessed March, 2020.
Unit 3: Dekker, Sidney. (2002) The field guide to human error investigations. Aldershot, UK: Ashgate Publishing.
Unit 3: Leape, L. "Error in medicine." Journal of the American Medical Association 272(23): 1851-57.
Unit 3: Reason, J.T, “Human error: models and management.” BMJ. 2000 Mar 18; 320(7237): 768–770.
Unit 3: Reason, J.T. (1990) Human error. Cambridge: Cambridge University Press.
Unit 3: Reason, J.T. (2001) "Chapter 1: Understanding adverse events: the human factor." In Charles Vincent, ed., Clinical risk management, 2nd ed. London, UK: British Medical Journal Books.
Unit 3: Wilson, B, “Causal factor tree analysis.” Retrieved from https://www.bill-wilson.net/root-cause-analysis/rca-tools/causal-factor-tree-analysis. Accessed March, 2020.
Unit 4: DeBono, E. (1993) Serious creativity: using the power of lateral thinking to create new ideas. New York, Harperbusiness.
Unit 4: Godfrey AB, Clapp TG, Nakajo T, et al. (2005) “Application of healthcare-focused error proofing: principles and solutions directions for reducing human errors.” Paper delivered at the ASQ World Conference on Quality and Improvement Proceedings, vol 59, Seattle.
Unit 4: Infinite Innovations, Ltd. “Brainstorming.” Retrieved from http://www.brainstorming.co.uk/tutorials/definitions.html. Accessed March, 2020.
Unit 5: Institute for Healthcare improvement. “Quality improvement essentials toolkit—run chart and control chart.pdf” Retrieved from http://www.ihi.org/resources/Pages/Tools/Quality-Improvement-Essentials-Toolkit.aspx. Accessed March, 2020.
Unit 5: Solberg L, Moser G, McDonald S. 1997. “The three faces of performance measurement: improvement, accountability, and research.” Jt Comm J Qual Improv. 23(3):135-47.
Unit 6: Institute for Healthcare Improvement. “Huddles.” Retrieved from http://www.ihi.org/resources/Pages/Tools/Huddles.aspx. Accessed March, 2020.
Supplemental Reading
Drickhamer, D. “View from the hospital floor: how to build a culture of improvement one unit at a time.” Lean Enterprise Institute. Retrieved from https://www.lean.org/common/display/?o=3207. Accessed March 2020.
Millard, M. “The top ten worst things you could do on a Gemba walk.” Krainexus. Retrieved from https://blog.kainexus.com/improvement-disciplines/lean/gemba-walk/the-top-ten-worst-things-you-could-do-on-a-gemba-walk. Accessed March, 2020.
You must log in and have started this course to submit a review.